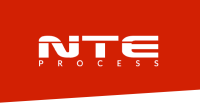
NOL-TEC EUROPE SRL - BULK MATERIAL HANDLING
RESEARCH, INNOVATION AND CUSTOMER CARE: THE KEY TO THE SUCCESS OF NTE PROCESS
NTE Process is a Single Source Provider that can drive its customers in all phases of design, supply and innovation of industrial plants thanks to patented proprietary technologies and international partners.
The NTE Process Research and Innovation Centre in Pessano con Bornago (Milan) is equipped with a 1:1 Pilot Plant to test the technologies in first person, perform both scientific tests (basic fluidity, aeration, consolidation, etc.) and full scale tests with customers' products (atomization, drying, solid-liquid mixing, parallel processing, pneumatic conveying, etc.). ) to best simulate the performance of the different technologies in real conditions and to have a predictive analysis of performance, energy consumption and all the details necessary for the correct design of industrial plants and complex technologies necessary for the development of increasingly high performance and customized raw materials and finished products.
"Customer caring is at the heart of our work: the process and design of each plant are defined and calibrated according to the specific needs of each customer. - explains Emanuele Fratto, Corporate Sales Manager NTE Process - We perform tests in the presence of our customers, we share videos and streaming, we provide detailed reports for performance analysis and preliminary plant design. But putting the customer at the center means more: we are particularly proud of our Customer Care service that assists our customers in the best management and maintenance of the plant".
One of the flagships solution of NTE Process - which has developed over 10 patents in recent years - is the dense phase pneumatic conveying system with Air Assist® technology: a latest generation solution that allows to optimize the control and speed of the products thanks to the use of Artificial Intelligence Air Assist® M533, strategically positioned along the conveying pipe. A choice that allows continuous monitoring of line pressure and flow; a reduction in air consumption (up to 70%*); an increase of system efficiency (+40%*); no product deterioration or segregation; self-diagnosis and self-learning systems.
* Results achieved on specific plant configurations.